摘要: 在高度為 10 m 循環流化床冷態試驗臺上,采用差壓法和積料法分別測定流化床爐膛顆粒濃度分布和物料循環流率,研究不同顆粒物料、在不同氣流速度爐內顆粒濃度分布特性和循環流率規律。研究表明循環流化床顆粒濃度沿爐膛高度方向呈現先急劇降低后緩慢減小的規律。對于一定的顆粒物料,爐膛氣流速度 ( 截面速度) 決定了爐膛稀相區區域物料濃度和和循環流化床鍋爐的固體物料循環流率。
人類大規模利用化石能源排放大量的溫室氣體被普遍認為是導致全球變暖的重要因素。我國的能源消費結構以煤為主,其中燃煤發電消耗煤量巨大,燃煤產生巨量的 CO 2 排放。目前 CO 2 的減排措施,一方面是通過提高煤炭利用效率達到少用煤減少 CO 2 排放目的,另一方面,對燃煤產生的CO 2 進行捕集,如富氧燃燒,煙氣中 CO 2 分離,然后對高濃度的 CO 2 進行壓縮、輸送、地下封存。然而,不管是采用富氧燃燒還是煙氣中 CO 2 分離措施,能耗均非常大,大規模應用幾乎不能接受,因此,近年來在 CO 2 捕集方面具有顯著低能耗優勢的化學鏈燃燒技術的研究進程明顯加速。
化學鏈燃燒是一種潔凈、高效新型無火焰燃燒技術。與傳統燃燒相比,該技術的#大優點是借助于中間載體在氧化 - 還原反應器間的循環,避免了燃料與空氣直接接觸,在化學轉化同時實現 CO 2 高效分離,在降低 CO 2 捕集能耗方面具有優勢;瘜W鏈燃燒工藝包括空氣反應器和燃料反應器,雙流化床反應器被認為是化學鏈燃燒#合適的反應器,其反應器中的燃料或載氧體流動狀態與循環流化床鍋爐爐膛內的固體顆粒的流動、循環類似。循環流化床鍋爐燃燒技術以燃燒效率高、環保特性好、調峰性能好、燃料適應性強等優點在電力行業獲得廣泛應用,技術已很成熟,為化學鏈燃燒技術發展奠定了良好基礎。
化學鏈燃燒的概念shou先由德國科學家 Richter1983 年提出,用來替代傳統燃燒提高火電廠熱效率; 1987 年日本學者 Ishida 與中國金紅光指出CLC 具有 CO 2 內分離的特性,并進行了實驗研究與理論分析,2004 年瑞典學者 Lyngfelt 等人實現了串行流化床化學鏈燃燒中試實驗,證明了化學鏈燃燒可以實現 CO 2 內分離。清華大學、東南大學、華中科技大學和華北電力大學在載氧體開發與測試以及小型試驗裝置運行方面進行相關研究。化學鏈燃燒動力系統已成為shijie能源領域研究的重要方向,是解決 CO 2 減排的主要發展的先金技術之一[1] 。
化學鏈燃燒/氣化技術應用了流化床技術,采用載氧體循環物料的化學鏈燃燒/氣化技術,爐膛顆粒濃度分布和循環流率等關鍵參數直接影響到爐內的氣固流動、燃燒/氣化反應、傳熱特性、磨損和產物生成特性,也是關系到化學鏈技術能夠實現工業化應用的關鍵所在[2 -4] 。本文在東方電氣東方鍋爐股份有限公司德陽基地試驗中心,采用爐膛內截面為 400 mm ×400 mm,爐膛高度 ( 距離布風板) 為 10 m 循環流化床試驗臺,以鈦鐵礦和循環灰為床料開展不同物料特性對流化床內顆粒濃度分布和物料循環流率影響規律試驗研究,為化學鏈燃燒/氣化技術工程化應用提供重要的技術支撐。
1 實驗裝置及方法
流化床冷態實驗系統主要包括爐膛、分離器、下降管、返料器、供風系統、引風系統、壓力采集系統、風量測量系統等。爐膛高度 ( 距離布風板)為10 m,布風板截面為280 mm ×400 mm,下爐膛變截面段高度為 900 mm,上部爐膛內截面為400 mm ×400 mm,下降管內圓直徑為 120 mm。為了保證流化床內部氣固流動的可視化,試驗部件均采用有機玻璃制成。實驗臺沿爐膛高度布置有 10 個壓力測點,旋風分離器出口和入口均布置 1 個壓力測點,下降管上布置有 4 個壓力測點,返料器上布置有 4 個壓力測點,返料腿上設置 1 個壓力測點,在爐膛一次風室、返料器的流化風室和返料風室分別布置 1 個壓力測點。采用
壓力變送器實時采集實驗臺各點的壓力值,利用壓差濃度法 ρ P = ΔP/ ( g × Δh 爐膛 ) 計算爐膛沿高度方向的顆粒濃度,其中 ρ P 為爐膛顆粒濃度 kg/m 3 ; ΔP 為相鄰兩側點壓力差 Pa;g 為重力加速度 m/s 2 ; Δh 爐膛 相鄰兩側點高度差 m。試驗過程中,由于流化床內物料湍流流動狀態極其強烈,爐膛內壓力值波動較大,測量壓力數據為穩定工況下,一分鐘內壓力測量數據的算術平均值。物料循環流率采用積料法測量,在實驗臺返料器上設置有回料截止閥,在系統穩定運行的瞬間截止回料,并測量物料在下降管的堆積速度,通過計算公式 Gs = ρ b × Δh 下降管 × S 下降管 / ( Ts ×S 爐膛 ) 計算循環流率,其中 Gs 為基于爐膛內截面積的物料循環流率 kg/ ( m 2 × s) ; ρ b 為物料顆粒的堆積密度 kg/m 3 Δh下降管 為下降管的堆積高度 m;S 下降管 為下降管的內截面積 m 2 ; S 爐膛 為爐膛的內截面積 m 2 ; 為物料顆粒堆積時間 s。
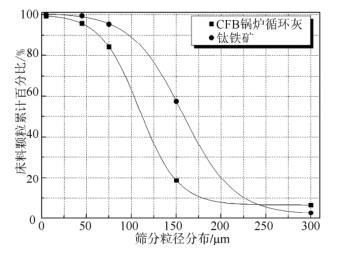
試驗物料采用鈦鐵礦和循環流化床鍋爐實際運行的循環灰,通過稱量測出其堆積密度分別為 2620 kg/m 3 、1 200 kg/m 3 。采用篩分裝置對鈦鐵礦和循環灰分別進行粒徑篩分 ( 見圖 1 ~ 2 所示) ,結果表明,鈦鐵礦粒徑范圍為 0μm ~ 300μm,D50中位粒徑約為 160μm,循環灰粒徑范圍是 0μm ~300μm,D50 中位粒徑為 110μm,且均符合玻爾茲曼分布規律 Y = A2 + ( A1 - A2) / ( 1 + EXP ( ( X- X0) /DX) ) ( Boltzmann Model) 。本次整個試驗在常溫常壓下進行,流化介質為空氣。
2 實驗結果與討論
2. 1 循環流化床試驗臺壓力分布
本次試驗分別采用鈦鐵礦和 CFB 鍋爐循環灰為床料,采用壓力傳感器和數據采集系統實時采集壓力變化。試驗在爐膛空截面速度 3. 6 m/s 下,采用鈦鐵礦 ( 靜止床料厚度 310 mm,床料量 97. 5kg) 和 CFB 鍋爐循環灰 ( 靜止床料厚度 490 mm,床料量60 kg) 的壓力分布趨勢如圖3 和圖4 所示。
試驗結果表明,采用合適粒徑分布的鈦鐵礦為物料,能夠實現在循環流化床冷態試驗臺的正常運行,且爐膛內壓力分布趨勢與采用循環灰為物料的運行狀況規律一致。從壓力分布曲線可看出,鈦鐵礦比 CFB 鍋爐循環灰堆積密度大得多,其單位堆積厚度的床壓降比 CFB 鍋爐循環灰高,在流化狀態下,運行床壓與床料密度和堆積厚度有關。
2. 2 截面速度對爐膛顆粒濃度的影響
圖 5 給出采用鈦鐵礦試驗床料,靜止爐膛高度為 310 mm ( 即床料量 58. 2 kg) ,不同截面速度下沿爐膛高度方向鈦鐵礦顆粒的濃度分布趨勢圖,整體而言,爐膛顆粒濃度沿爐膛高度方向均呈現逐漸降低的趨勢,且顆粒濃度在 h/H =0. 045 以下的爐膛區域急劇下降,在 h/H =0. 045 以上的爐膛區域緩慢下降,其中 h 為爐膛壓力測點高度,H 為爐膛總高度;
在試驗截面速度范圍內 ( 2. 5 m/s → 3. 6 m/s) ,爐膛密相區 ( h = 0 ~ 3 500 mm) 和稀相區 ( h =3 500 mm ~10 000 mm) 壓降與截面速度的關系曲線見圖 6,由曲線可知隨著截面速度增加爐膛密相區的壓差呈現下降趨勢 ( 5 800Pa → 5 035 Pa) ,爐膛稀相區差壓值呈現上升趨勢 ( 122Pa → 715 Pa) ,表明,隨著截面速度升高,爐膛密相區床料充氣膨脹更強烈,氣/固比升高,而稀相區壓差隨截面速度的升高而升高,說明氣體對鈦鐵礦顆粒的攜帶能力增強。
2. 3 截面速度對循環流率的影響
圖 7 給出采用鈦鐵礦為試驗床料,靜止爐膛高度分別為190 mm、400 mm、470 mm ( 即對應床料量分別 58. 2 kg、128. 3 kg、153. 2 kg) ,不同截面速度與循環速率的趨勢圖。由圖可知,對不同床料量鈦鐵礦而言,隨著爐膛截面流速的升高,單位爐膛截面的循環流率增大。圖 8 給出采用 600MW 超臨界 CFB 鍋爐燃煤機組的循環灰為試驗床料,靜止爐膛高度分別為 295 mm、410 mm、490mm ( 即對應床料量分別 27. 3 kg、45. 7 kg、60. 0kg) ,不同截面速度與循環速率的趨勢圖。由圖可知,不同靜止爐膛高度的循環灰循環流率與爐膛截面速度均呈現線性關系。
2. 4 爐膛差壓與循環流率的關系
對循環流化床鍋爐,工程上通常采用爐膛差壓值間接反映鍋爐循環速率大小。由圖 9 可知針對鈦鐵礦床料而言,在稀相區高度段 ( 即 ΔH 3 =3 500 mm ~ 9 760 mm) 爐膛差壓與循環流率的一元線性相關系數 r = 0. 96,呈現線性關系。對循環灰床料而言,稀相區高度段 ( 即 ΔH 3 = 3 500 mm~ 9 760 mm) 爐膛差壓與循環流率的一元線性相關系數 r = 0. 91,呈現線性關系。整體趨勢上看,循環灰的爐膛差壓與循環流率一元線性關系與采用鈦鐵礦類似,且兩者一元線性的斜率和相關系數 r 存在一定差異,造成上述差異原因與床料顆粒從分離器出口物料損失速率、床料顆粒在爐膛內的氣/固比等因素差異有關 ( 注: 分離器出口幾乎沒有鈦鐵礦顆粒物料損失,而循環灰顆粒有不同程度物料損失) 。
2. 6 不同物料顆粒對循環流率的影響
本文采用物料粒徑范圍為 0μm ~ 300 μm 鈦鐵礦( D50 =160 μm,ρ b =2 620 kg/m 3 ) 和循環灰( D50=110 μm,ρ b =1 200 kg/m3 ) 床料開展冷態試驗研
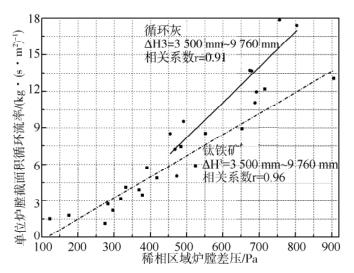
究,圖 10 給出了不同物性床料顆粒的爐膛靜止床料質量與循環流率關系圖。由圖可知,爐膛靜止床料質量約60kg,爐膛截面風速為2. 8 m/s 時,循環灰顆粒循環流率為 11. 09 kg/( s × m 2 ) 明顯高于鈦鐵礦顆粒的循環流率 2. 70 kg/( s × m 2 ) ; 爐膛截面風速為 3. 6 m/s 時,循環灰顆粒循環流率為17. 40 kg/( s × m 2 ) 明顯高于鈦鐵礦顆粒的循環流率4. 92 kg/( s × m 2 ) ,即循環灰的循環流率明顯高于
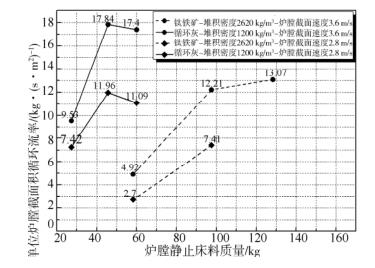
鈦鐵礦的循環流率。導致該現象的主要原因是兩種床料顆粒密度、粒徑分布和物性參數等存在差異,鈦鐵礦真實密度 ρ P = 5 000 kg/m 3 ,堆積密度ρ b =2 620 kg/m 3 ,D50 =160 μm,循環灰真實密度ρ P =2 500 kg/m 3 ,堆積密度 ρ b =1 200 kg/m 3 ,D50=110 μm,#終造成兩種床料顆粒的流化特性( 相同物料量和流化速度) 存在一定程度的差異。
3 結 語
由上述分析計算可得能下結論。
( 1) 采用合適粒徑分布的鈦鐵礦為物料,能夠實現在循環流化床冷態試驗臺的正常運行,且爐膛內壓力分布趨勢與采用循環灰為物料的運行狀況規律一致。
( 2) 本次試驗的鈦鐵礦顆粒濃度沿爐膛高度方向均呈現逐漸降低趨勢,顆粒濃度在 h/H = 0. 045以下爐膛區域急劇下降,在 h/H =0. 045 以上爐膛區域緩慢下降,其中 h 為爐膛壓力測點高度,H 為爐膛總高度。試驗表明,隨著截面速度升高,氣體對鈦鐵礦顆粒的攜帶能力逐漸增強,且密相區和稀相區的中間位置約為 h =3 500 mm( 即 h/H =0. 35) 。
( 3) 本次試驗鈦鐵礦和循環灰兩種顆粒均隨著爐膛截面流速的升高,單位爐膛截面的循環流率增大; 在相同物料量和流化速度下,循環灰的循環流率明顯高于鈦鐵礦的循環流率。
( 4) 鑒于本次試驗條件下的鈦鐵礦顆粒的循環流率偏低,可能會影響到熱態試驗臺爐內傳熱和溫度場分布,因此實際化學鏈反應器設計時還需要進一步優化鈦鐵礦粒徑分布、靜止床層物料高度 ( 床內存料量) 、選擇合適運行速度 ( 爐膛截面速度) ,以及考慮有效防磨措施。